Heating elements for tool moulds and pressing
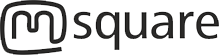
Direct heating of moulds accelerates and simplifies the manufacturing process of fiber composite components. The energy input is significantly lower, and the savings in energy costs are immense.
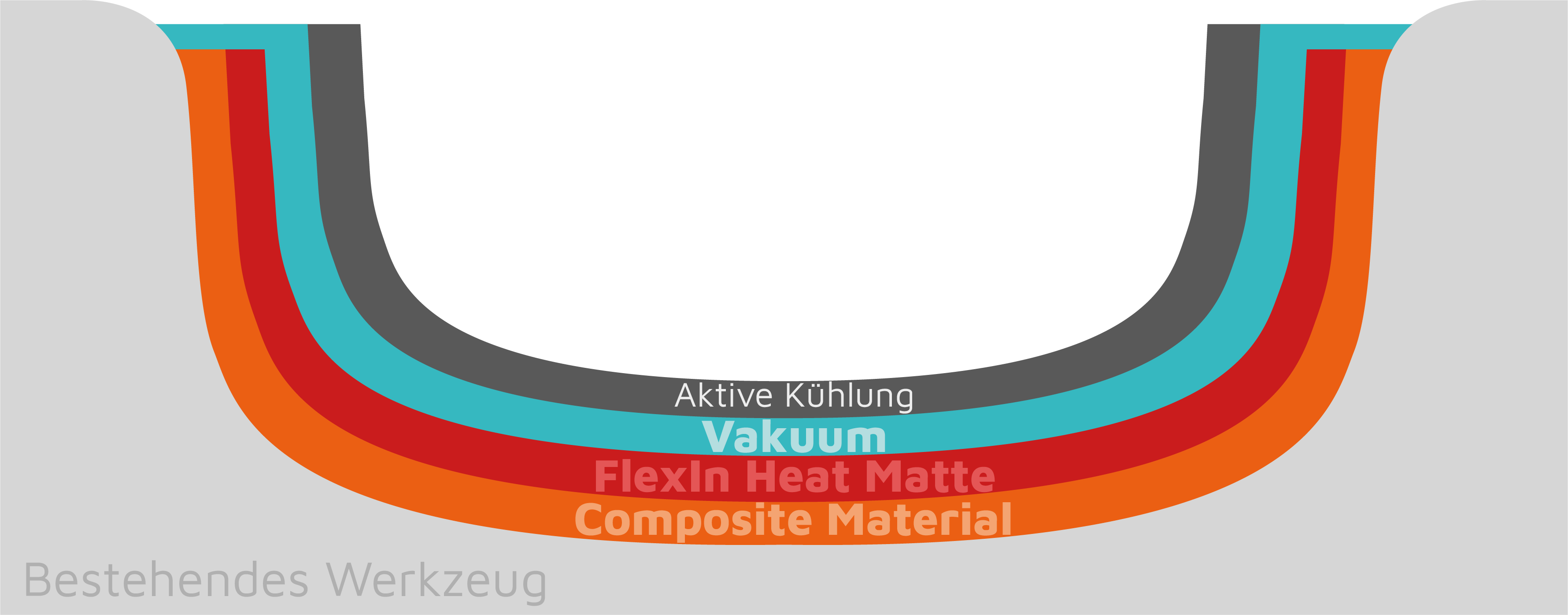
Mould making
Appropriate moulds (negative or positive mould) are required for the production of components made of fibre composites. These are usually made quickly and inexpensively from epoxy resin and reinforcing fibres.
The usual structure is one with a top layer of mold resins, which forms the mould surface, and a fibre-reinforced back layer with laminating resins, which is responsible for the rigidity and strength of the manufactured mould.
The low-shrinkage epoxy resin used creates very precise moulds, which in turn enable dimensionally accurate component production.
Types of mould construction:
Mould construction with GFRP:
A classic buildup consists of a top layer of mould resin, a thin coupling layer and edge fill with a thixotropic and lightly filled laminating resin, and a backer of glass fabric or scrim also in combination with laminating resin.
A quasi-isotropic and symmetrical laminate structure ensures a very low-stress laminate and thus effectively prevents distortion.
Layers of graduated basis weight (from light to heavy) additionally prevent the fabric or scrim structure from showing on the mould surface. Moulds produced in this way can be used at temperatures up to about 120 °C, depending on the resin system used.
Mould making with CFRP:
Carbon fabric - or scrims - is used in the rear end when moulds have to withstand higher temperatures while exhibiting identical thermal expansions to the CFRP components manufactured in them. Here, too, a quasi-isotropic and symmetrical structure ensures a very low-stress laminate that does not undergo any significant change in length even at temperatures above 100 °C, since carbon fibres exhibit a slightly negative thermal expansion in the fibre direction. Depending on the resin system used, very precise moulds can thus be built up to approx. 200 °C process temperature.
Mould making with laminating and casting ceramics:
Mould making with laminating and casting ceramics is used when thick-walled moulds are to be built up cost-effectively and in a short time. In this process, cover layers of mold resin are combined with a backing of a liquid, synthetic hard-shell gypsum in conjunction with a fiber reinforcement of a voluminous glass mat complex. The moulds produced in this way can be used at process temperatures of up to approx. 50 °C.u